FAQ
The distinction and use of different grades of stainless steel
Release time:2025-07-04
The different grades of stainless steel are mainly distinguished by their chemical composition and metallographic structure, and their properties and application scenarios have their own focuses. The following are the differences and uses of the main classifications and typical grades:
1、 Classified by metallographic structure and typical grades
Austenitic stainless steel
Characteristics: Non magnetic (may have weak magnetism after cold processing), excellent corrosion resistance, good plasticity and toughness, easy to weld and process.
Typical brand:
304 (06Cr19Ni10): containing 18-20% chromium and 8-10% nickel, widely used in tableware, kitchenware, building decoration, etc.
316 (06Cr17Ni12Mo2): Adding 2-3% molybdenum significantly improves the resistance to chloride ion corrosion, suitable for seawater equipment, chemical reactors, and medical devices.
316L: Low carbon version (carbon ≤ 0.03%), with stronger resistance to intergranular corrosion after welding, used for thick walled welded parts and nuclear industry equipment.
Ferritic stainless steel
Characteristics: Magnetic, better resistance to chloride stress corrosion than austenitic steel, but poor plasticity and cannot be strengthened by heat treatment.
Typical brand: 430
Containing 12-14% chromium, used in low corrosion environments such as building decoration and home appliance casings.
Martensitic stainless steel
Characteristics: Magnetic, can adjust hardness and strength through heat treatment, but has weak corrosion resistance.
Typical brand:
410/420: Used for high hardness components such as cutting tools and bearings.
440 series: High carbon and high hardness, manufacturing high-end cutting tools and surgical instruments.
Dual phase stainless steel (austenitic ferritic)
Characteristics: It combines austenite toughness and ferrite strength, and has excellent resistance to chloride ion corrosion.
Typical brand: 329
Used for chemical pipelines, seawater treatment equipment, etc.
Precipitation hardening stainless steel
Characteristics: Obtaining high strength and hardness through precipitation hardening treatment.
Typical brand: 630 (17-4PH)
Used for aviation parts, springs, and high-strength mechanical components.
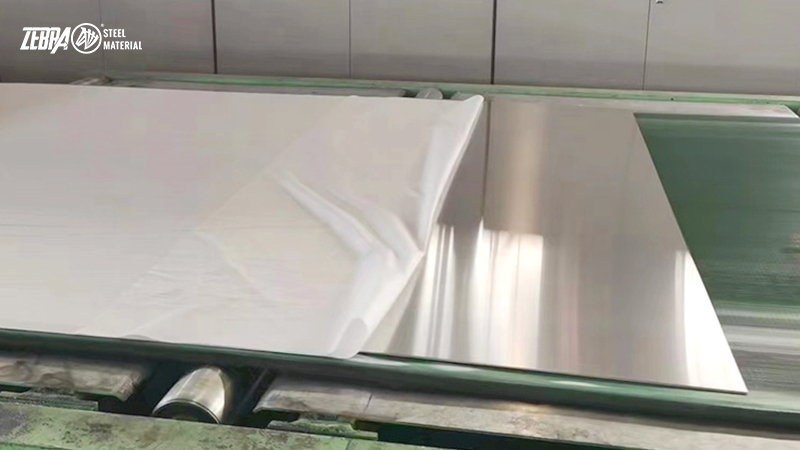
2、 Key performance comparison and application selection
Recommended types of performance requirements, typical application scenarios
High corrosion resistance, non-magnetic: austenitic steel (304/316) (food equipment, medical devices)
Corrosion resistance to chloride ions: Molybdenum containing austenitic steel (316) (for seawater desalination equipment and chemical storage tanks)
High hardness and wear resistance: Martensitic steel (440) (tool, bearing)
High strength+corrosion resistance: precipitation hardened steel (630) (aviation fasteners, springs)
Low cost, weakly corrosive environment: ferritic steel (430) (doors, windows, automotive exhaust pipes)
Stress corrosion cracking resistance: Dual phase steel (329) (chemical pipelines, offshore platforms)
3、Special precautions
Low carbon version (such as 304L/316L):
Carbon content ≤ 0.03%, reduces the risk of intergranular corrosion after welding, suitable for welding structural components.
Food grade requirements:
304 may not necessarily meet food grade standards and must comply with heavy metal migration restrictions (such as GB 4806.9).
Common Misconceptions:
The size of the number does not directly represent the performance (such as 430 having lower corrosion resistance than 304).
In summary, the selection of stainless steel grades should be based on a comprehensive consideration of corrosion environment, mechanical requirements, and cost. Austenitic steel has the widest applicability, and special environments require targeted material selection.